Well, it's been a while since a bit of good news has come my way with my engine problems, but, after sitting down with my engineer and making a plan for the rebuild I can safely say that the full reassembly is now a week away (ish) 
After having the crankshaft reground at both the main and big end bearings by one step oversize we did a sample reassembly using new bearings to accurately measure the deck height. Using a base support plate of apparently 1.00 mm (actually 1.25mm) the deck height came out at -0.51mm added to this was the Head gasket of 0.50mm thickness giving us a squish area of 1.01 mm
This is toward the high end of the recommended range (range being 0.9144mm to 1.143mm or 36 to 45 thou in old money
) There is some room to manoeuvre on these figures but it is largely dependant on cam and combustion chamber size. As my Cam is 35/75-75/35 (290) and my chamber sizes are 34.2cc and 35.7cc I was looking at 10:1 C/R for a reliable fast road set up.:devil: It was found that due to a squish step that was cut into my 34.2cc head (see pic) this made it difficult to fit a gasket without disturbing the squish action as the piston came up to TDC so the only reason is this head has been altered to run without a gasket. But if we removed the gasket the C/R would reach over 11:1 and cause the squish band performance to go below the minimum figure of 0.9144mm - Back to square 1 
My other head - later Panda 30, still has the gas ring and the original chamber profile, but has been skimmed slightly to give 35.7cc capacity. If we ran with the 1.25mm base plate and used an 81.5mm bore gasket of 0.5mm thickness this would give around 9.8:1 C/R with an acceptable squish area from the head capacity. So result!! 

As part of the balancing exercise we are checking the piston and conrod weights to equalise them prior to balancing the crank. I intend to include the rear pulley and flywheel with clutch pressure plate too. I'll get back with balancing news when I have it.
Ian.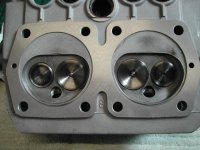
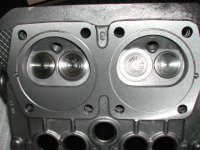
Ian.
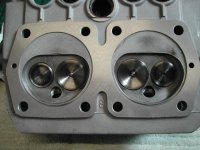
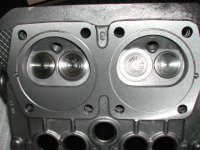