Well there's some nice alternatives there and it comes down to price, whether you want to try to do it in situ or on the bench and whether you want to make a one off or a career out of it
Hydraulic is nice and controlled. Screw threads are easy to replace
They'll all need that spacer in the end to make the bush go fully home of course.
Plates and screws made up might cost as little as £30 from an engineering shop
The first step for me would be to reduce the bush outside diameter to a correct interference fit tolerance and I'd probably have that done at a machine shop too prior to doing the job. It's the understandable time factor when the bushes have already failed and you just want to get it back on the road so I might just get some bushes already and have them done at my local engineers. That's what we're all discussing here, getting prepared for when it does happen so we dont get caught out
What I don't like/ understand is the twisting rotary force the bush is subjected to in use. It's a silentbloc, designed to reduce noise/vibration like an engine mount and yet, as suspension sags and shock absorbers wear out, then it will be subjected to constant internal twisting if the centre bolt allows no turning action. It would explain why the MW suffer the most and why the bushes can fail again so quickly after renewal. Whereas a 3 door carrying very little load in the back might last so much longer mileage
Now if someone said that's it's vital to torque the centre bolt lightly enough so that it still allows some rotary movement in the bush that would make some sense. Or if the bush allowed rotation without severe internal flexing it would be nice. But for all of it to be failrly rigid I can't see what the plan is?
What is the torque for the bush centre bolt?
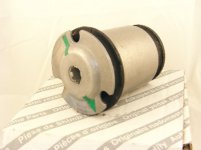
Why does the bush centre hole have cutouts/ serrations? Is that to allow some settling or twisting?
What is the purpose of the three slots?