Last stage of primer...
By this time we have blocked our filler coats out with
36 and then 80 grit, then sprayed poly and blocked with 180 grit, sprayed again and blocked with 220 and 320, and now we will block this 2k Urethane primer with 320 then 400 and finally 600 to be ready to paint....I say we are custom sanders not custom painters.
However that is the easy sanding, after we clear it, I sand with a small hand block every inch of the car starting at 600 and up from there, 800,1000,1200,1500,2000,2500 and then using a Dual Actions sander 2500 and 3000. I am ready at that point to cut/buff with a wool pad, then a foam cutting pad, then a black polish pad, and finally a blue polish pad. My arms ache just thinking about it.
We upgraded the front to disc brakes....
After we inspect and clean and inspect and clean...she is ready for the no going back part...sealer primer. I mix a quick close match to the final color...once sprayed I have about 1.5 hours to spray my base coat.
Getting ready to spray is a lot of work, you have a window of time from the last wet sanding with 600 before you have to scuff the body again....my product time window is about 6 hours...you can imagine then that sanding this car inside and out, every place paint will be sprayed is a all day job for even 2 men. Then the time to clean it and inspect it and mask it all off is quite a bit as well..so you end up having to go back and scuff the body with a grey scotch brite pad before actually spraying any sealer primer or base..... I found myself spraying the basecoat at 9pm Friday so I came back and finished with the last 2 coats in the morning. You have a little more time between coats with the base coat. The sealer must be topcoated with base within 1.5 hours or you have to scuff the car again.
Base...
Clear coat....5 coats...
We start assembly and sanding....all the main components, engine,transaxle, chrome and seats are due in the shop this week.
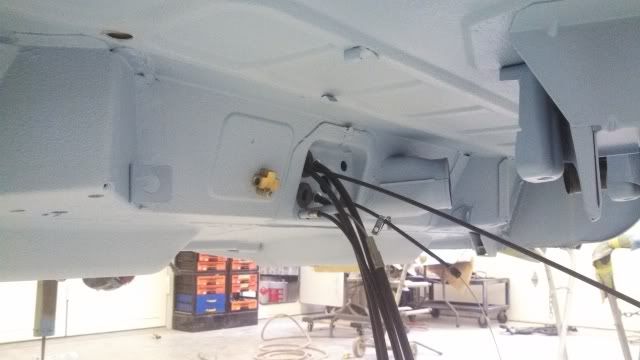