Following on from my comments on welding in the thread "Jacks and Axle Stands" earlier in this section, here, for your delectation, is a wee guide to my first welding machine. My guess would be that I bought it in the 70's because I thought I would be able to replace wings and do MOT corrosion repairs with it at home. How wrong I was! Anyway here's the machine:
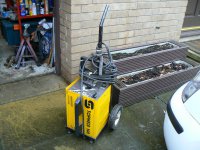
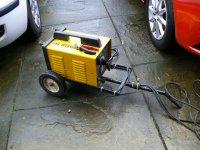
As you can plainly see, it's an SIP 140 Topweld. After finding out I couldn't weld thin sheet with it (actually that's not strictly true. You can if you are particularly skilled at cadence welding and use very small rods - a hopeless task for a beginner) I parked it under my work bench and forgot about it for years. Then I made friends with a welding instructor and when he heard I had the machine he shamed me into learning how to use it and, more importantly, what I could reasonably aspire to weld with it. After a couple of weeks of messing about with every spare bit of angle iron and flatstock I could find, he set me the job of making a wheelie cradle for it. The very one you can see in the pictures above. It was the start of my love affair with this machine which continues to this day. Just look at these welds:
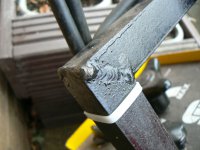
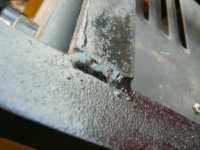
Not bad for a novice eh? Well Ok, penetration leaves a bit to be desired and maybe they're not all that symmetrical and "pretty" looking but they've lasted being heaved in and out of the back of vans, cars and trailers for maybe 50 years?
These cheap machines do have a few drawbacks though and one is that they don't have very good duty cycles. By that I mean that if you weld anything substantial with them, needing a bit of current to get the melt/penetration, they tend to get too hot. Ultimately, without protection, you could face a meltdown and ruined machine. Luckily the manufacturers install thermal cut outs on them which shuts down the power when it gets too hot. That's fine but it takes ages for the core to cool back to a working temperature and then not long for it to get too hot again! This is called "Duty Cycle". A machine with a 100% duty cycle would mean that you could just weld for ever and it wouldn't cut out 50% means you can weld for 50% of the total time (ie, crudely speaking, 5 mins welding 5 mins idle). This didn't affect me at all when I was learning as I never welded for long enough for the machine to overheat. However as I got better I would occasionally experience it - not too often though as I seldom would run a bead longer than 2 or 3 inches continuously before stopping to locate and clamp the next piece in place- (like when I was welding up the chassis of my trailer.)
So, what to do about it? Well lets have a look inside:
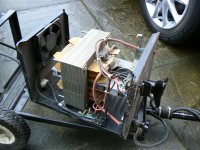
Not really that much is there? A sodding great laminated core with lots of heavy duty ALUMINIUM wire wrapped round it - It's a transformer folks! By the way, more about the aluminium wire later. Look carefully at the next picture and you'll see there is a long screw threaded rod running into the laminated core? This rod goes through the front plate and has a big black hand wheel on it's end.
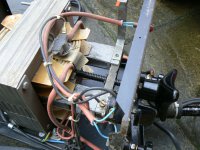
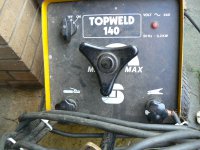
Not so clear, but you can see the guides each side, is the "slug" which this screwed rod can push into, and withdraw from, the middle of the laminated core. This is how it controls the output current available. Withdraw the "slug" and you reduce the density of the core and so reduce the magnetic flux. Insert the "slug" and the density increases so the flux goes up. It's this massive laminated core which gets hot. Look now at the actual windings and sitting on top of them you'll see a smallish black plastic thing with 2 wires. This is the Thermal cut out which, if the core gets too hot, cuts the power and stops the electricity to the core coils.
My solution? fit a fan:
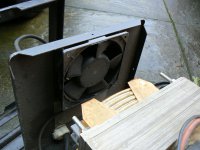
and baffle the casing so the air is directed to flow over the core and cool it - Air comes in at both sides on the front and is forced to exit at the back by the fan:
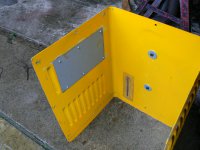
Since doing this mod I can't remember it ever cutting out!
Let's get back to those aluminium windings. If you can find a machine with copper windings jump on it. First off it was always the better quality and more expensive machines that had/have copper windings. The aluminium works well as a conductor but there is a problem with the connectors. Look here:
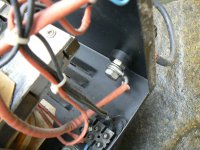
The aluminium wire is connected to a steel terminal! OOPs! ever heard of electrolytic corrosion? Yup, I've dismantled and cleaned mine off at least a couple of times over the years. The effect is really insidious. slowly you will find the arc is getting harder to strike and weld penentration problems manifest themselves. The reason, of course, is that the poor connection is reducing any given current for a known setting on the machine. This is very likely to be present on an older machine and may well be why it's for sale. You can often bag an absolute bargain because of it. A quick clean up and you're good to go! By the way, similar things can happen to the outside cable terminals:
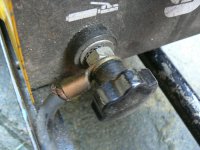
Make sure everything is tight. We are using high currents here and loose connections mean high resistance and problems for you.
Then there's the current selection for welding with any given size of rod. On the outside case some machines have a pointer for guidance:
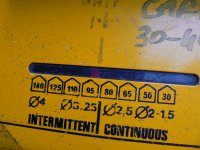
Inside the machine you can see the pointer is simply fixed to the sliding "slug":
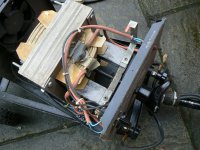
The scale should be considered to be only the very roughest of guides. The current needed is only loosely ruled by the rod size. It's more a function of how much current is needed to generate sufficient heat for any particular workpiece to give the weld a good melt and penetration with minimum distortion due to too much heat input. If the pointer and it's scale have not been damaged/ distorted/removed you can use it as a rough starting point but you are almost crtainly going to need to fine tune to get a quality result.
On the subject of rods. These small machines are quite fussy, ask for a rutile rod when buying and you'll find them best to learn on. As you can see from the pictures, my machine claims to be able to "burn" 1.5, 2, 2.5, 3.25, and 4 mm diameter rods. All those years ago I bought a whole box of 1.6mm rods - I still have 2/3 of the box unused - 2mm? I've never seen 2mm rods for sale? but I'd be happy to buy if there was a special offer. 2.5mm are my rod of choice and I used them to build the trailer and on just about all I do. 3.25? yes I've got a pack - only half used though. The machine burns them with the current screwed right up but you can't burn more than a couple of rods before the thermal cutout calls it a day and you need to go off and do something else for half an hour or so. 4mm? good luck with them. Never bought any, mind you I don't weld anything that needs such a beast of a rod. If I run into something a bit thicker that I feel could do with extra support I just do multi runs. Here's a 1.6 a 2.5 and a 3.25 just for comparison:
Oh, and don't forget your welders cap, worn back to front under your helmet:
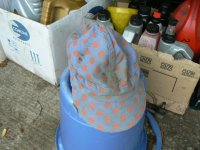
Here's some of the things I just saw lying around in the garage which were welded with this machine using 2.5 rods:
Trailer tailgate hinges and a chassis joint on the extreme right
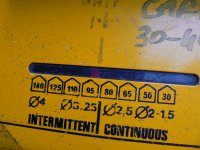
An "A" frame for my Hi Lift jack.
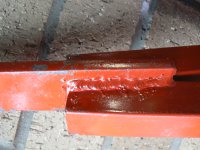
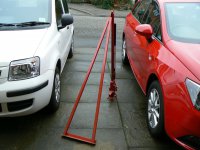
Makes it easier pulling fence posts and uprooting shrubs which it does in just minutes
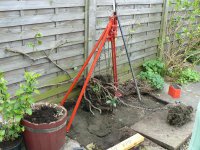
PS sorry guys. I missed out putting in the picture of the welding rods. Sure you can imagine what some pieces of wire of different thickness look like? Something went wrong with the trailer tailgate pic too. I'm never going to master these darn computery things am I?
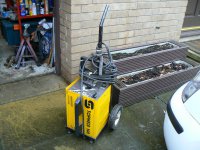
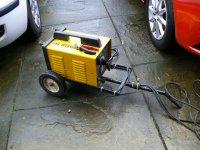
As you can plainly see, it's an SIP 140 Topweld. After finding out I couldn't weld thin sheet with it (actually that's not strictly true. You can if you are particularly skilled at cadence welding and use very small rods - a hopeless task for a beginner) I parked it under my work bench and forgot about it for years. Then I made friends with a welding instructor and when he heard I had the machine he shamed me into learning how to use it and, more importantly, what I could reasonably aspire to weld with it. After a couple of weeks of messing about with every spare bit of angle iron and flatstock I could find, he set me the job of making a wheelie cradle for it. The very one you can see in the pictures above. It was the start of my love affair with this machine which continues to this day. Just look at these welds:
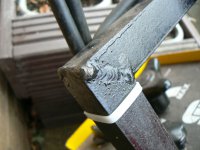
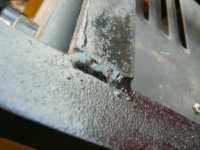
Not bad for a novice eh? Well Ok, penetration leaves a bit to be desired and maybe they're not all that symmetrical and "pretty" looking but they've lasted being heaved in and out of the back of vans, cars and trailers for maybe 50 years?
These cheap machines do have a few drawbacks though and one is that they don't have very good duty cycles. By that I mean that if you weld anything substantial with them, needing a bit of current to get the melt/penetration, they tend to get too hot. Ultimately, without protection, you could face a meltdown and ruined machine. Luckily the manufacturers install thermal cut outs on them which shuts down the power when it gets too hot. That's fine but it takes ages for the core to cool back to a working temperature and then not long for it to get too hot again! This is called "Duty Cycle". A machine with a 100% duty cycle would mean that you could just weld for ever and it wouldn't cut out 50% means you can weld for 50% of the total time (ie, crudely speaking, 5 mins welding 5 mins idle). This didn't affect me at all when I was learning as I never welded for long enough for the machine to overheat. However as I got better I would occasionally experience it - not too often though as I seldom would run a bead longer than 2 or 3 inches continuously before stopping to locate and clamp the next piece in place- (like when I was welding up the chassis of my trailer.)
So, what to do about it? Well lets have a look inside:
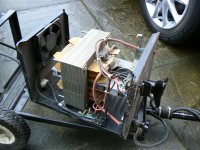
Not really that much is there? A sodding great laminated core with lots of heavy duty ALUMINIUM wire wrapped round it - It's a transformer folks! By the way, more about the aluminium wire later. Look carefully at the next picture and you'll see there is a long screw threaded rod running into the laminated core? This rod goes through the front plate and has a big black hand wheel on it's end.
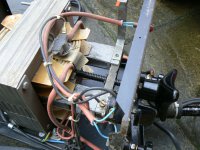
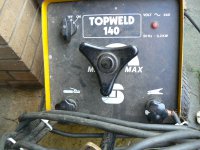
Not so clear, but you can see the guides each side, is the "slug" which this screwed rod can push into, and withdraw from, the middle of the laminated core. This is how it controls the output current available. Withdraw the "slug" and you reduce the density of the core and so reduce the magnetic flux. Insert the "slug" and the density increases so the flux goes up. It's this massive laminated core which gets hot. Look now at the actual windings and sitting on top of them you'll see a smallish black plastic thing with 2 wires. This is the Thermal cut out which, if the core gets too hot, cuts the power and stops the electricity to the core coils.
My solution? fit a fan:
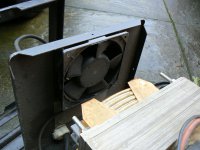
and baffle the casing so the air is directed to flow over the core and cool it - Air comes in at both sides on the front and is forced to exit at the back by the fan:
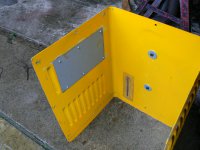
Since doing this mod I can't remember it ever cutting out!
Let's get back to those aluminium windings. If you can find a machine with copper windings jump on it. First off it was always the better quality and more expensive machines that had/have copper windings. The aluminium works well as a conductor but there is a problem with the connectors. Look here:
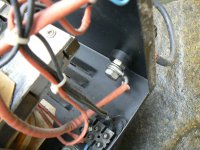
The aluminium wire is connected to a steel terminal! OOPs! ever heard of electrolytic corrosion? Yup, I've dismantled and cleaned mine off at least a couple of times over the years. The effect is really insidious. slowly you will find the arc is getting harder to strike and weld penentration problems manifest themselves. The reason, of course, is that the poor connection is reducing any given current for a known setting on the machine. This is very likely to be present on an older machine and may well be why it's for sale. You can often bag an absolute bargain because of it. A quick clean up and you're good to go! By the way, similar things can happen to the outside cable terminals:
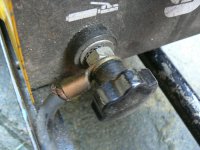
Make sure everything is tight. We are using high currents here and loose connections mean high resistance and problems for you.
Then there's the current selection for welding with any given size of rod. On the outside case some machines have a pointer for guidance:
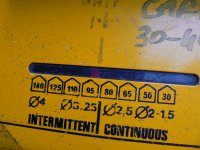
Inside the machine you can see the pointer is simply fixed to the sliding "slug":
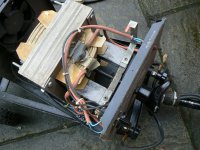
The scale should be considered to be only the very roughest of guides. The current needed is only loosely ruled by the rod size. It's more a function of how much current is needed to generate sufficient heat for any particular workpiece to give the weld a good melt and penetration with minimum distortion due to too much heat input. If the pointer and it's scale have not been damaged/ distorted/removed you can use it as a rough starting point but you are almost crtainly going to need to fine tune to get a quality result.
On the subject of rods. These small machines are quite fussy, ask for a rutile rod when buying and you'll find them best to learn on. As you can see from the pictures, my machine claims to be able to "burn" 1.5, 2, 2.5, 3.25, and 4 mm diameter rods. All those years ago I bought a whole box of 1.6mm rods - I still have 2/3 of the box unused - 2mm? I've never seen 2mm rods for sale? but I'd be happy to buy if there was a special offer. 2.5mm are my rod of choice and I used them to build the trailer and on just about all I do. 3.25? yes I've got a pack - only half used though. The machine burns them with the current screwed right up but you can't burn more than a couple of rods before the thermal cutout calls it a day and you need to go off and do something else for half an hour or so. 4mm? good luck with them. Never bought any, mind you I don't weld anything that needs such a beast of a rod. If I run into something a bit thicker that I feel could do with extra support I just do multi runs. Here's a 1.6 a 2.5 and a 3.25 just for comparison:
Oh, and don't forget your welders cap, worn back to front under your helmet:
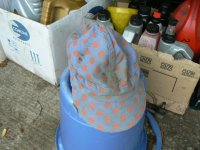
Here's some of the things I just saw lying around in the garage which were welded with this machine using 2.5 rods:
Trailer tailgate hinges and a chassis joint on the extreme right
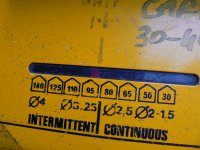
An "A" frame for my Hi Lift jack.
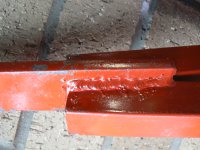
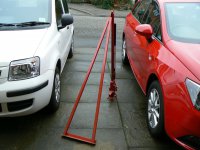
Makes it easier pulling fence posts and uprooting shrubs which it does in just minutes
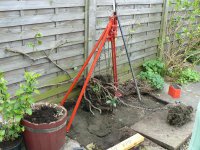
PS sorry guys. I missed out putting in the picture of the welding rods. Sure you can imagine what some pieces of wire of different thickness look like? Something went wrong with the trailer tailgate pic too. I'm never going to master these darn computery things am I?
Last edited: