So a Punto mk2 head won't fit a Punto mk1 engine? Wrong. Here's how, in text and snapshots.
The Punto mk1 has been around for 20 years, and the supply of cars in scrapyards has now diminished sharply, making cheap spares hard to come by. Into this category comes the cylinder head, feebly clamped down with 10 stretchy bolts, a complex angle-tightening procedure, and leak-prone.
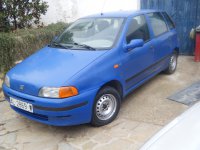
I had endless trouble with the head gasket on my 1994 mk1 Punto 55 1100cc, and having decided on a replacement cylinder head, discovered that I could not locate a mk1 car in any nearby scrapyard. So I settled for a mk2 head from a low-mileage 1242cc car, and set about making it fit.
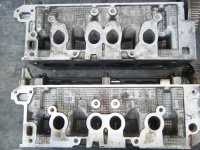
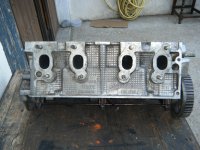
The differences between the mk1 and the mk2 head are as follows:-
1. Intake side stud patterns differ markedly, also mk2 has 1 extra stud.
2. The mk2 has no water temperature switch nor the threaded hole required.
3. The cam belt pulley has a different tooth pitch.
4. Intake port shapes differ slightly because of 4 injectors on the mk2, of no importance.
5. Other casting differences, of no importance.
The similarities making this swap feasible are as follows:-
1. Exhaust side stud pattern is the same.
2. Cambox cover bolt pattern is the same.
3. Cylinder head bolt pattern is the same.
4. Coil mount is the same.
5. Camshaft, valves and combustion chambers look the same or are very similar.
An adapter plate is required made from 9/16" black mild steel (BMS) plate, bored for the inlet ports to exactly correspond, and drilled and tapped so that it fits between the mk2 head and the mk1 inlet manifold. This is fixed using longer studs plus some extra studs and 2 gaskets, sandwiched between the head and the manifold. I did consider adapting the injector unit onto the mk2 airbox, but discarded the idea as impractical. The mk2 air box is very nasty and not a suitable starting point.
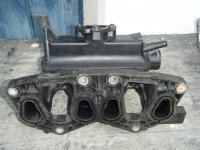
The snapshots show the job proceeding in stages, from head removal to job finished. The two snaps of the top surface of the block show it before and after tapping out from 9mm to 10mm, once I had decided on this modification. Not many will want this option, it is likely to introduce problems lifting the head at a later date, due to the 10 thick studs required. However it works well. The studs and nuts required for this mod cost no more than new head bolts at Fiat prices.
The method is as follows:-
1. Ready the mk2 head by routine head prep work. Check and record all valve clearances. Remove the camshaft, shims, buckets, retainers, collets and valves, and store them carefully in sequence. Remove the valve stem seals and discard. Lightly rub the valves into the seats with fine carborundum paste to restore a good seal. Do not overdo this, so your valve clearances remain unchanged. Rebuild with new camshaft and valve stem seals, then check that valve clearances are within book tolerance. Fit mk1 camshaft pulley in place of mk2.
2. The BMS steel plate MUST be smooth, clean and FLAT, and large enough in length and width to cover all the required stud holes and water ports. New BMS will be flat enough and will have a smooth blue glazed surface. Mine was left behind by some careless lift engineers on a building site in Carboneras, where I was pumping readymixed concrete. Check for flatness by passing a long clean mill file over both sides, showing high and low spots. Ease down any high spots. Do not imagine that 8mm studs will squeeze 9/16" BMS flat if it isn't already! I used 9/16" BMS because that's what turned up, but 1/2" BMS would do just as well.
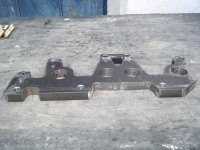
3. Careful measurements, checking and rechecking, and thinking about what each hole does before drilling, will pay dividends during the hand fitting that follows. Only drill or cut when you have checked 3 times what you are doing it for, and where! Avoid enlarging holes until it is absolutely necessary, you don't want the manifold to be able to move around on the studs, any more than necessary for ease of assembly. When enlarging a hole slightly off-centre, a chain saw file may be better than drilling an oversized hole. Lightly countersink all finished holes except tapped holes.
4. The lower 3 stud holes are in the same position on both mk1 and mk2 heads. They constitute your baseline and datum for all subsequent marking-out. All others are different and have to be carefully marked out before drilling. The mk2 inlet manifold is plastic and moulded with wide tolerances, and may be heat distorted. It is useless for accurate marking-out, so chuck it away before it gets you into trouble! There is no mk2 gasket available to help you here. Using mk1 inlet manifold as a template, mark the 3 holes along the bottom onto your piece of BMS and centre punch these holes. Do not get too near the edge of the plate. Drill the holes for clearance on 8mm studs. Using 8mm rod to locate the manifold via these 3 holes, mark the upper 4 mk1 manifold stud holes, centre punch, and drill and tap for 8mm studs.
5. On the mk2 head, using a scribing compass located on the 3 datum stud holes, establish positions for the upper 4 mk2 manifold studs, and transfer them to the BMS by scribing intersecting arcs. Centre-punch where they cross and drill clearance holes for 8mm studs. There is 1 extra stud above the water passage from head to manifold, mark it using the temperature sensor from the mk2 head, drill clearance hole for an 8mm stud. Using old gaskets to establish these hole positions will get you into much trouble! All studs must be ACCURATELY marked, eyeball before drilling! in your BMS You will now have 8 holes clearance on 8mm, and 4 holes tapped 8mm.
6. Using a discarded mk1 manifold gasket, mark the 4 inlet port positions onto the BMS plate, being careful to datum the gasket with the 3 baseline studs. Find the centre of each port using crossed scribed lines, then scribe the required circles using the gasket as a general guide, leaving the exact positions of the ports scribed deeply on the BMS plate. Centre punch in suitable places around the ports marked, so that you can drill slightly overlapping holes around the port inside the scribed circle, and release the centre. Do not overlap much or the drill will wander. Drill a few large holes rather than many small ones. A large round file and a carbide burr will remove metal not drilled out, to leave smooth ports in exactly the positions required. Check your work repeatedly against the mk2 head and the mk1 inlet manifold, filing to get a smooth transition across the joints. A pillar drill, sharp cobalt drill bits, and a new fine-tooth long round file about 3/4" diameter will help here. Finish the ports round and smooth, and chamfer slightly. An expanding reamer if available will leave a professional finish. Mark and drill 2 overlapping holes for the passage where the water flows from head to mk1 manifold. File to the correct shape.
7. Place the mk1 manifold onto the BMS plate located by the 3 datum stud holes, and scribe around the outside edge of the casting. This reveals unwanted metal which needs to be removed to provide clearance for a sparking plug socket and the plug wire boots. Drill large holes in the corners, remove metal with thin cutting wheels on your angle-grinder, then a carbide burr and sharp files will leave a neat finish with chamfered edges. There is no short cut but it takes less time than you think. Think before drilling and cutting, it pays dividends, and will shorten the time and effort required. Do not cut off the lugs left for studs on the mk2 head!
8. To achieve easy assembly make many trial fits. Some holes may need to be drilled or filed out slightly, or elongated. New studs 9/16" longer will be needed in most positions. The originals will suffice in 4 cases. These 4 studs screwed into your adapter plate MUST NOT protrude the other side! Use washers and original nuts if available. Do not be tempted to use bolts. After trial fitting, paint the adapter before final assembly. Screw in the studs using Loctite if you prefer.
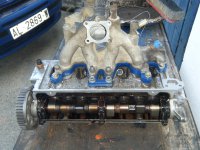
9. Establish location of the water temperature switch threaded hole on your mk1 head, and centre-punch the mk2 head at this point. Drill and tap 3/8" BSP. There is a welch plug in the front of the head in this position, be careful your drill and tap clears this, it will be very close. Screw your mk1 switch into this hole with sealant.
10. Assemble on the bench using 2 new fibre inlet manifold gaskets, if you can obtain them. I had to use pressed steel ones, in Spain the fibre type are unobtainable. Smear with Hylomar jointing paste before assembly, and allow to dry. Tighten all nuts evenly and progressively, but do not overtighten. Before bolting down the head assembly to the block, insert the 2 hollow locating dowels and place the head in position with no gasket. If it rocks then the dowels are too long! Shorten them until the head seats flat. Then assemble with a GOOD head gasket and Hylomar jointing compound. And I know what the books say about that! Paint the Hylomar on with a small brush and allow to dry. It does not seal the fire-rings, but works well for the water passages.
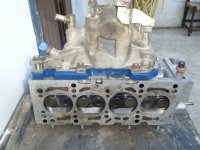
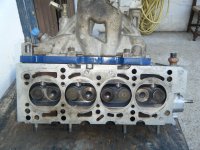
11. You will have to straighten your dipstick to clear, as there is now less room behind the head. Use the mk1 cambelt cover, the mk2 cover will not fit no matter how you hack it about. The spring clip securing the air filter body to the camshaft cover is now 9/16" too short, leave it off, it does very little. The air filter is now 9/16" further back but still clears the relay and fuse box behind. The breather hose from cambox cover to air filter is also 9/16" too short, fit a longer one. And get rid of that stupid Fiat rubber oil cap, get a proper one like mine! (Easygrip for Case front-end loader)
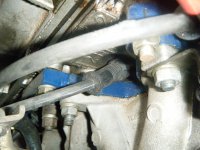
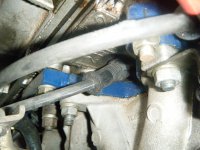
12. As an afterthought I made and fitted a stepped trunnion block for the stud above the water passage. The manifold on a mk1 head is only clamped by 1 stud at this point. This trunnion drilled 8mm and carefully measured, cut and filed to shape, will locate on the lip of the casting at this point, and squeeze the shim gasket more tightly, also clamping the adapter plate to the head. A worthwhile extra for the steel shim gasket.
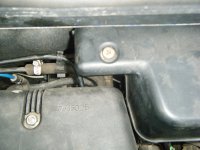
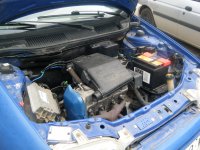
13. You might like to consider an additional mod, to add belt and braces. Remember that racing and road haulage engines do not use head bolts, they use studs and shoulder nuts. You will not find head bolts on any serious road haulage engine. Some use individual heads with studs, shoulder nuts and bridge-pieces, the best system.
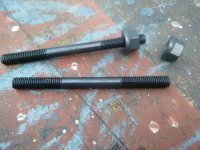
14. Plug the cylinder bores at half-stroke tightly with plenty of rags. The joke stretchy head bolts are only 9mm diameter, and are designed for robot and not human assembly. They provide insufficient clamping force via a too-small 13mm head and 19mm shoulder. If one of these snaps off below the surface, you are in big trouble!
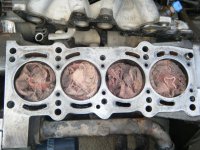
15. Tap the holes in the block out to 1.5mm x 10mm with a long good quality bottoming tap, no pilot drill is needed. Get as far down as you can without breaking the tap, clearing swarf regularly. Blow out the holes with compressed air. Squirt clean alcohol down the holes, allow to soak for an hour, blow out again and let dry. Using a few drops of loctite screw in 1.5mm x 10mm x 125mm alloy steel studs with rolled threads, which are commercially available (try Weston Tooling). Make sure they all bottom in the holes and that the locating dowels are in place.
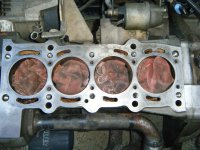
16. Make sure there is thread visible right down to the nut seats and for at least 2 threads below. Using a thin-wall 17mm 3/8" sq. drive socket which you will have to grind down due to lack of room, clamp the head down with 1.5mm x 10mm shoulder nuts having a 17mm flat and a 22mm shoulder. Grease the stud threads and do not use washers. I torqued them down to 50, 65 and finally 75 ft.lbs. You have just put your head gasket troubles to bed FOR GOOD!
I am not an engineer, nor a mechanic, just a concrete-mixer driver self-taught by necessity in vehicle maintenance. Anyone who can use hand tools can tackle the above job with every expectation of success. My car has since run 1 year with no water loss, and performance is unaffected. Change your refrigerant every 2 years at least and buy a new expansion tank cap.
Roland Brindley
The Punto mk1 has been around for 20 years, and the supply of cars in scrapyards has now diminished sharply, making cheap spares hard to come by. Into this category comes the cylinder head, feebly clamped down with 10 stretchy bolts, a complex angle-tightening procedure, and leak-prone.
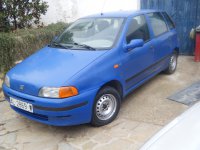
I had endless trouble with the head gasket on my 1994 mk1 Punto 55 1100cc, and having decided on a replacement cylinder head, discovered that I could not locate a mk1 car in any nearby scrapyard. So I settled for a mk2 head from a low-mileage 1242cc car, and set about making it fit.
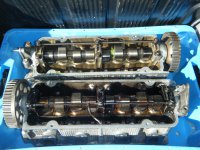
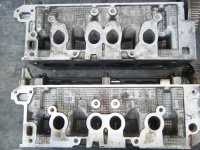
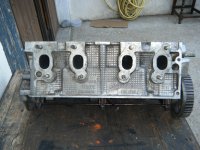
The differences between the mk1 and the mk2 head are as follows:-
1. Intake side stud patterns differ markedly, also mk2 has 1 extra stud.
2. The mk2 has no water temperature switch nor the threaded hole required.
3. The cam belt pulley has a different tooth pitch.
4. Intake port shapes differ slightly because of 4 injectors on the mk2, of no importance.
5. Other casting differences, of no importance.
The similarities making this swap feasible are as follows:-
1. Exhaust side stud pattern is the same.
2. Cambox cover bolt pattern is the same.
3. Cylinder head bolt pattern is the same.
4. Coil mount is the same.
5. Camshaft, valves and combustion chambers look the same or are very similar.
An adapter plate is required made from 9/16" black mild steel (BMS) plate, bored for the inlet ports to exactly correspond, and drilled and tapped so that it fits between the mk2 head and the mk1 inlet manifold. This is fixed using longer studs plus some extra studs and 2 gaskets, sandwiched between the head and the manifold. I did consider adapting the injector unit onto the mk2 airbox, but discarded the idea as impractical. The mk2 air box is very nasty and not a suitable starting point.
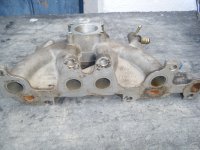
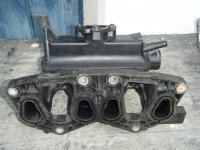
The snapshots show the job proceeding in stages, from head removal to job finished. The two snaps of the top surface of the block show it before and after tapping out from 9mm to 10mm, once I had decided on this modification. Not many will want this option, it is likely to introduce problems lifting the head at a later date, due to the 10 thick studs required. However it works well. The studs and nuts required for this mod cost no more than new head bolts at Fiat prices.
The method is as follows:-
1. Ready the mk2 head by routine head prep work. Check and record all valve clearances. Remove the camshaft, shims, buckets, retainers, collets and valves, and store them carefully in sequence. Remove the valve stem seals and discard. Lightly rub the valves into the seats with fine carborundum paste to restore a good seal. Do not overdo this, so your valve clearances remain unchanged. Rebuild with new camshaft and valve stem seals, then check that valve clearances are within book tolerance. Fit mk1 camshaft pulley in place of mk2.
2. The BMS steel plate MUST be smooth, clean and FLAT, and large enough in length and width to cover all the required stud holes and water ports. New BMS will be flat enough and will have a smooth blue glazed surface. Mine was left behind by some careless lift engineers on a building site in Carboneras, where I was pumping readymixed concrete. Check for flatness by passing a long clean mill file over both sides, showing high and low spots. Ease down any high spots. Do not imagine that 8mm studs will squeeze 9/16" BMS flat if it isn't already! I used 9/16" BMS because that's what turned up, but 1/2" BMS would do just as well.
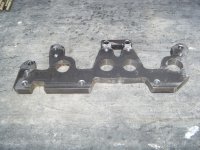
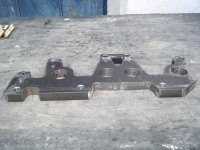
3. Careful measurements, checking and rechecking, and thinking about what each hole does before drilling, will pay dividends during the hand fitting that follows. Only drill or cut when you have checked 3 times what you are doing it for, and where! Avoid enlarging holes until it is absolutely necessary, you don't want the manifold to be able to move around on the studs, any more than necessary for ease of assembly. When enlarging a hole slightly off-centre, a chain saw file may be better than drilling an oversized hole. Lightly countersink all finished holes except tapped holes.
4. The lower 3 stud holes are in the same position on both mk1 and mk2 heads. They constitute your baseline and datum for all subsequent marking-out. All others are different and have to be carefully marked out before drilling. The mk2 inlet manifold is plastic and moulded with wide tolerances, and may be heat distorted. It is useless for accurate marking-out, so chuck it away before it gets you into trouble! There is no mk2 gasket available to help you here. Using mk1 inlet manifold as a template, mark the 3 holes along the bottom onto your piece of BMS and centre punch these holes. Do not get too near the edge of the plate. Drill the holes for clearance on 8mm studs. Using 8mm rod to locate the manifold via these 3 holes, mark the upper 4 mk1 manifold stud holes, centre punch, and drill and tap for 8mm studs.
5. On the mk2 head, using a scribing compass located on the 3 datum stud holes, establish positions for the upper 4 mk2 manifold studs, and transfer them to the BMS by scribing intersecting arcs. Centre-punch where they cross and drill clearance holes for 8mm studs. There is 1 extra stud above the water passage from head to manifold, mark it using the temperature sensor from the mk2 head, drill clearance hole for an 8mm stud. Using old gaskets to establish these hole positions will get you into much trouble! All studs must be ACCURATELY marked, eyeball before drilling! in your BMS You will now have 8 holes clearance on 8mm, and 4 holes tapped 8mm.
6. Using a discarded mk1 manifold gasket, mark the 4 inlet port positions onto the BMS plate, being careful to datum the gasket with the 3 baseline studs. Find the centre of each port using crossed scribed lines, then scribe the required circles using the gasket as a general guide, leaving the exact positions of the ports scribed deeply on the BMS plate. Centre punch in suitable places around the ports marked, so that you can drill slightly overlapping holes around the port inside the scribed circle, and release the centre. Do not overlap much or the drill will wander. Drill a few large holes rather than many small ones. A large round file and a carbide burr will remove metal not drilled out, to leave smooth ports in exactly the positions required. Check your work repeatedly against the mk2 head and the mk1 inlet manifold, filing to get a smooth transition across the joints. A pillar drill, sharp cobalt drill bits, and a new fine-tooth long round file about 3/4" diameter will help here. Finish the ports round and smooth, and chamfer slightly. An expanding reamer if available will leave a professional finish. Mark and drill 2 overlapping holes for the passage where the water flows from head to mk1 manifold. File to the correct shape.
7. Place the mk1 manifold onto the BMS plate located by the 3 datum stud holes, and scribe around the outside edge of the casting. This reveals unwanted metal which needs to be removed to provide clearance for a sparking plug socket and the plug wire boots. Drill large holes in the corners, remove metal with thin cutting wheels on your angle-grinder, then a carbide burr and sharp files will leave a neat finish with chamfered edges. There is no short cut but it takes less time than you think. Think before drilling and cutting, it pays dividends, and will shorten the time and effort required. Do not cut off the lugs left for studs on the mk2 head!
8. To achieve easy assembly make many trial fits. Some holes may need to be drilled or filed out slightly, or elongated. New studs 9/16" longer will be needed in most positions. The originals will suffice in 4 cases. These 4 studs screwed into your adapter plate MUST NOT protrude the other side! Use washers and original nuts if available. Do not be tempted to use bolts. After trial fitting, paint the adapter before final assembly. Screw in the studs using Loctite if you prefer.
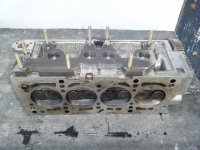
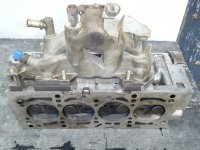
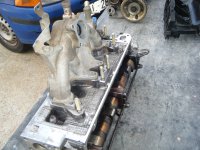
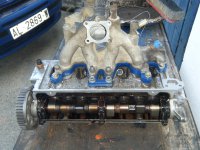
9. Establish location of the water temperature switch threaded hole on your mk1 head, and centre-punch the mk2 head at this point. Drill and tap 3/8" BSP. There is a welch plug in the front of the head in this position, be careful your drill and tap clears this, it will be very close. Screw your mk1 switch into this hole with sealant.
10. Assemble on the bench using 2 new fibre inlet manifold gaskets, if you can obtain them. I had to use pressed steel ones, in Spain the fibre type are unobtainable. Smear with Hylomar jointing paste before assembly, and allow to dry. Tighten all nuts evenly and progressively, but do not overtighten. Before bolting down the head assembly to the block, insert the 2 hollow locating dowels and place the head in position with no gasket. If it rocks then the dowels are too long! Shorten them until the head seats flat. Then assemble with a GOOD head gasket and Hylomar jointing compound. And I know what the books say about that! Paint the Hylomar on with a small brush and allow to dry. It does not seal the fire-rings, but works well for the water passages.
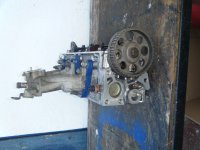
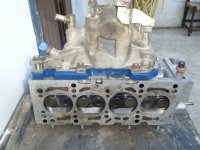
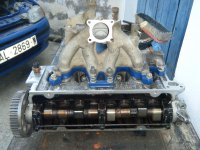
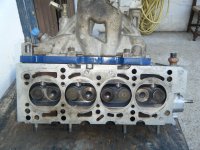
11. You will have to straighten your dipstick to clear, as there is now less room behind the head. Use the mk1 cambelt cover, the mk2 cover will not fit no matter how you hack it about. The spring clip securing the air filter body to the camshaft cover is now 9/16" too short, leave it off, it does very little. The air filter is now 9/16" further back but still clears the relay and fuse box behind. The breather hose from cambox cover to air filter is also 9/16" too short, fit a longer one. And get rid of that stupid Fiat rubber oil cap, get a proper one like mine! (Easygrip for Case front-end loader)
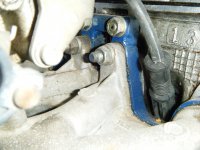
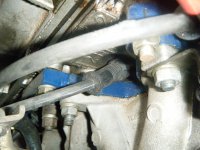
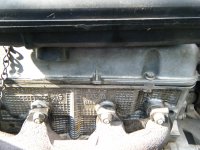
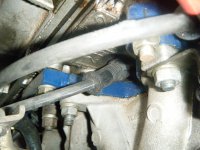
12. As an afterthought I made and fitted a stepped trunnion block for the stud above the water passage. The manifold on a mk1 head is only clamped by 1 stud at this point. This trunnion drilled 8mm and carefully measured, cut and filed to shape, will locate on the lip of the casting at this point, and squeeze the shim gasket more tightly, also clamping the adapter plate to the head. A worthwhile extra for the steel shim gasket.
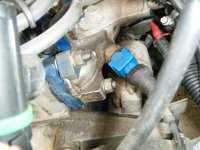
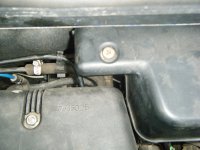
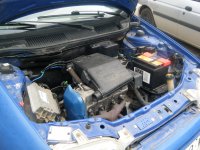
13. You might like to consider an additional mod, to add belt and braces. Remember that racing and road haulage engines do not use head bolts, they use studs and shoulder nuts. You will not find head bolts on any serious road haulage engine. Some use individual heads with studs, shoulder nuts and bridge-pieces, the best system.
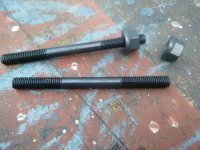
14. Plug the cylinder bores at half-stroke tightly with plenty of rags. The joke stretchy head bolts are only 9mm diameter, and are designed for robot and not human assembly. They provide insufficient clamping force via a too-small 13mm head and 19mm shoulder. If one of these snaps off below the surface, you are in big trouble!
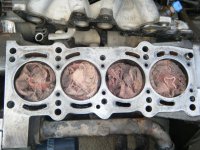
15. Tap the holes in the block out to 1.5mm x 10mm with a long good quality bottoming tap, no pilot drill is needed. Get as far down as you can without breaking the tap, clearing swarf regularly. Blow out the holes with compressed air. Squirt clean alcohol down the holes, allow to soak for an hour, blow out again and let dry. Using a few drops of loctite screw in 1.5mm x 10mm x 125mm alloy steel studs with rolled threads, which are commercially available (try Weston Tooling). Make sure they all bottom in the holes and that the locating dowels are in place.
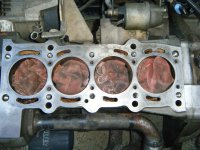
16. Make sure there is thread visible right down to the nut seats and for at least 2 threads below. Using a thin-wall 17mm 3/8" sq. drive socket which you will have to grind down due to lack of room, clamp the head down with 1.5mm x 10mm shoulder nuts having a 17mm flat and a 22mm shoulder. Grease the stud threads and do not use washers. I torqued them down to 50, 65 and finally 75 ft.lbs. You have just put your head gasket troubles to bed FOR GOOD!
I am not an engineer, nor a mechanic, just a concrete-mixer driver self-taught by necessity in vehicle maintenance. Anyone who can use hand tools can tackle the above job with every expectation of success. My car has since run 1 year with no water loss, and performance is unaffected. Change your refrigerant every 2 years at least and buy a new expansion tank cap.
Roland Brindley