This is about sorting out holes that a spot weld drill has caused but it just as easily sorts any manner of large holes where really you'd like metal
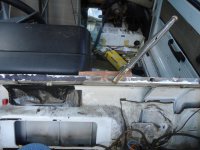
So what we are looking at is the windscreen frame, a hole and a piece of copper tube hammered flat, held in place with Molegrips.
You can't weld to copper. Or more exactly welding is joining two similar materials by melting them together and that don't happen with steel mig wire and copper.
So our flattened tube absorbs loads of heat and acts as a platform to build up an nice blob of weld without getting anything stuck to it.
Like magic, grind down the weld blob and.........
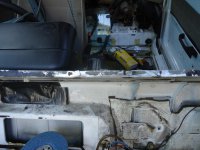
Fantastic. Better to have a thicker piece of copper but this will do.
It also works if you are wanting to butt weld very thin stuff. The copper acting as a heat sink.
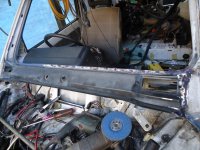
After a couple of hours of trimming fitting, trimming fitting etc etc, this is Ronnies panel welded in place. A wipe of filler to keep everything smooth and I can paint it tommorow night and hopefully refit the windscreen on Saturday.
And to think some people waste valuable garage time watching TV
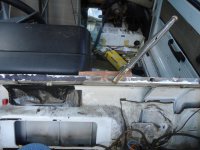
So what we are looking at is the windscreen frame, a hole and a piece of copper tube hammered flat, held in place with Molegrips.
You can't weld to copper. Or more exactly welding is joining two similar materials by melting them together and that don't happen with steel mig wire and copper.
So our flattened tube absorbs loads of heat and acts as a platform to build up an nice blob of weld without getting anything stuck to it.
Like magic, grind down the weld blob and.........
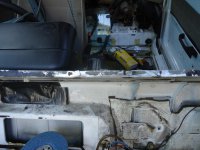
Fantastic. Better to have a thicker piece of copper but this will do.
It also works if you are wanting to butt weld very thin stuff. The copper acting as a heat sink.
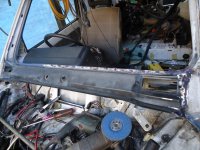
After a couple of hours of trimming fitting, trimming fitting etc etc, this is Ronnies panel welded in place. A wipe of filler to keep everything smooth and I can paint it tommorow night and hopefully refit the windscreen on Saturday.
And to think some people waste valuable garage time watching TV
Last edited by a moderator: