So of the more astute members might recognise this one.
Suffice to say that the last ower did lots of work which turned into a kind of 'Forth Bridge' scenario and ultimately lost heart.
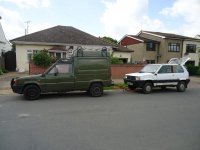
It's an old rusty 4x4 that isn't quite ready to be turned into Coke cans just yet.
I must confess that my original intention was to build a 6x4 Panda but due to pressure of projects it will probably just get fixed. Oh yeah and my wife said I mustn't 6 wheel it. Ah another car and another time.
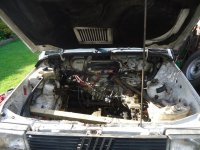
First obvious issue is the fact that there is no engine.
Not a problem. The late 'Purple Ronnie' happily donated a running injection example and fitted with an Ebay rescue carb'd head it will continue to provide service.
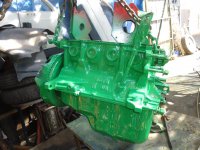
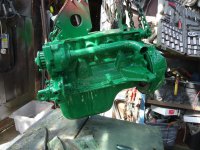
Yes it is a hideous colour but I had a big tin of Rustoleam left over from something else.
There are obvious rust issues
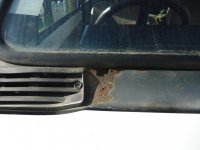
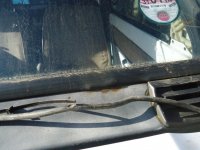
With yet another successfull screen removal I found this.
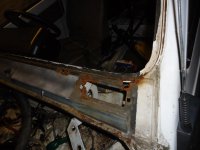
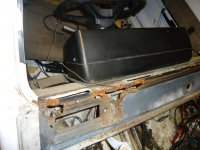
Fortunately 'Purple Ronnie' donated this
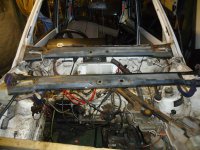
That will be a perfect condition scuttle panel then.
Suffice to say that the last ower did lots of work which turned into a kind of 'Forth Bridge' scenario and ultimately lost heart.
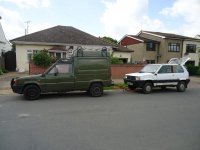
It's an old rusty 4x4 that isn't quite ready to be turned into Coke cans just yet.
I must confess that my original intention was to build a 6x4 Panda but due to pressure of projects it will probably just get fixed. Oh yeah and my wife said I mustn't 6 wheel it. Ah another car and another time.
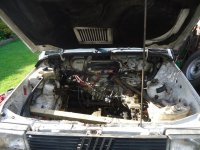
First obvious issue is the fact that there is no engine.
Not a problem. The late 'Purple Ronnie' happily donated a running injection example and fitted with an Ebay rescue carb'd head it will continue to provide service.
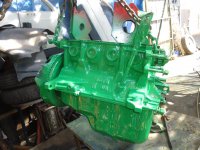
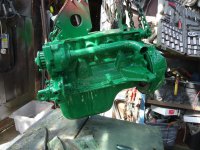
Yes it is a hideous colour but I had a big tin of Rustoleam left over from something else.
There are obvious rust issues
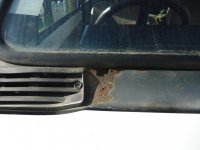
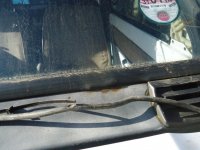
With yet another successfull screen removal I found this.
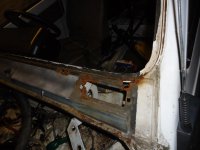
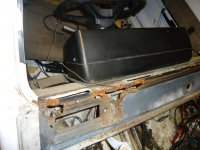
Fortunately 'Purple Ronnie' donated this
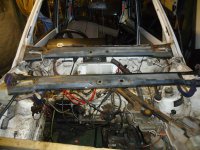
That will be a perfect condition scuttle panel then.
Last edited by a moderator: